鈦冶金通常采用氯化冶金的方式從鈦鐵礦或富鈦料中將鈦元素以四氯化鈦形式提取出來,再根據(jù)下游產品選擇還原或是氧化來生產金屬鈦或者氧化鈦。而鈦的氯化冶金根據(jù)其反應的不同主要分為熔鹽氯化和沸騰氯化兩種。
沸騰氯化由于其具有產能大、不產生廢鹽等優(yōu)勢,是近年來四氯化鈦生產的主流工藝,尤其是國際上的氯化法鈦白粉生產技術均是采用沸騰氯化法生產工藝。鈦冶金過程的沸騰氯化主要在沸騰氯化爐內進行,而內襯材料則是沸騰氯化爐重要的組成部分,是關系到其能否正常使用和運行的關鍵。
一、氯化爐內襯結構簡介
整個沸騰氯化爐內襯的主要作用是形成氣流邊界,形成撞擊流的約束,使得物料合理流態(tài)化。并在高溫反應下起到隔熱、絕熱的作用。在整個運行過程中,氯化爐內成分十分復雜,主要成分為:高鈦渣顆粒,TiCl4、Cl?、O?、CO、CO?、N?等。沸騰氯化爐主要分為以下幾個部分:
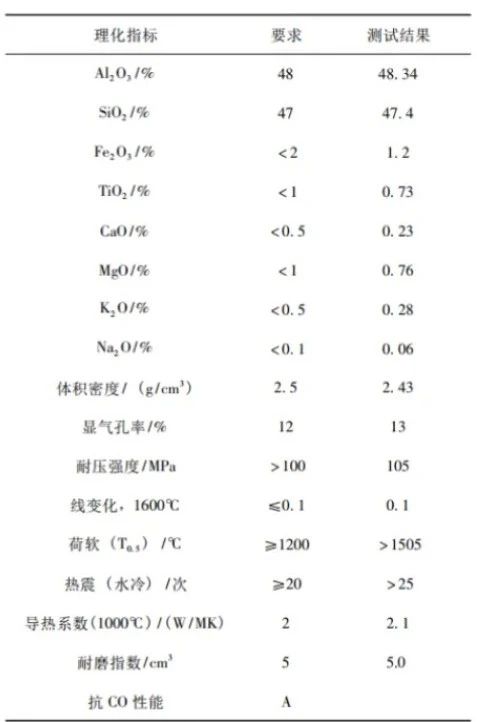
圖1 氯化爐示意圖
(一)爐底和反應段
由于沸騰氯化爐的特殊結構,氯氣進氣口主要安裝在該段,均勻地分布在四周。在通入氣體后,形成撞擊流,在爐底和四周內襯的約束下,形成向上的流態(tài)化反應床層。爐底和反應段內襯正常工作溫度為900~1000℃,這一區(qū)域主要承受爐料在撞擊流作用下的直接沖擊和摩擦作用。該部位因承受物料的沖擊、上升的磨損氣體侵入、碳沉積發(fā)生反應而容易發(fā)生內襯材料的損壞。其損壞原因主要有:
1、熱的作用:即熱負荷、熱沖擊;
2、化學作用:由于氯氣、堿金屬、渣等化學元素的侵入,造成內襯材料渣化和損壞,以及氯氣與耐火材料的化學作用;
3、機械作用:由于物料顆粒的摩擦和含塵煙氣磨損造成內襯材料的受損。
(二)進料段
在該部分周期地進料(依據(jù)工藝而定),特別在進料口中采用了特殊的材料,以減少固體顆粒物的磨損。但由于工藝的操作,反應段的升降,大量的流態(tài)化高溫流對該部分的內襯的沖刷是主要的破壞因素,特別是進料口附近的內襯是沖刷厲害的部位。
1、過渡段。過渡段在反應段與爐底之間起過渡作用,該部位的溫度在800℃左右,過渡段爐襯主要與未反應的物料接觸,受到物料的侵蝕作用并不大。
2、擴大段。沸騰氯化爐上部是用于降低氣流速度,而使得未反應的物料在重力作用下返回至反應段繼續(xù)進行反應,有效利用物料。
二、氯化爐內襯損壞機理分析
(一)爐襯材料的成份及礦物組成
沸騰氯化爐內襯材料主要采用Al?O?和SiO?,物相組成主要為莫來石,主要化學成份及物理性能測試見表1。
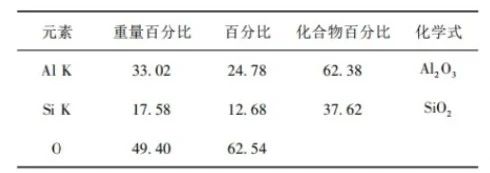
表1 氯化爐爐襯材料要求及測試分析結果
(二)氯化爐爐襯材料損壞過程研究
從熱力學上看,Al?O?-SiO?系材料[4]各物相在氯化反應中:莫來石相(A?S?)非常不穩(wěn)定,其成份見表2,石英相(SiO?)非常穩(wěn)定,剛玉相(Al?O?)居中;在碳熱還原中:石英相非常不穩(wěn)定,剛玉相非常穩(wěn)定,莫來石相居中。在實際中,爐襯材料是如何損壞的,其過程是怎樣發(fā)生的,這要從殘磚顯微結構分析入手。
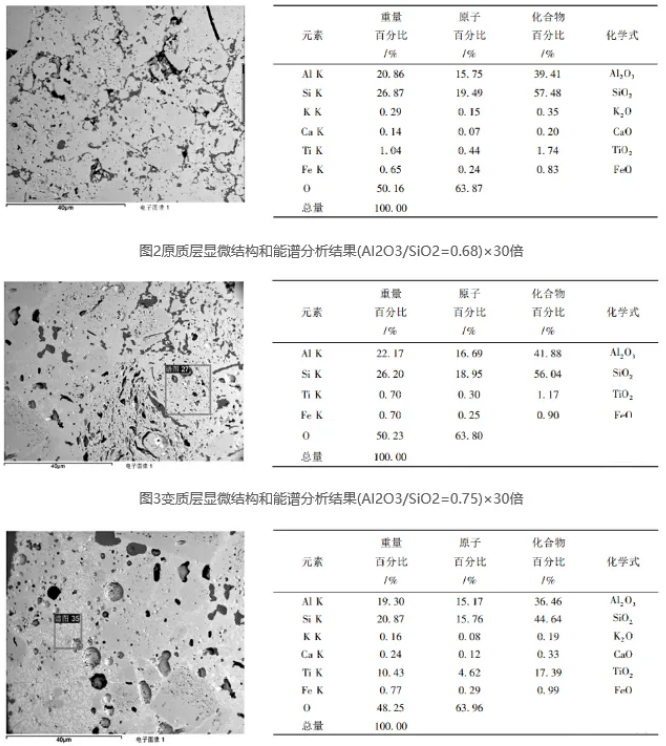
表2 莫來石成分
取氯化爐內殘磚,按原磚層、變質層、反應層切片,采用6300SEM電子顯微鏡,能譜采用OXFORD硅鋰檢測器,對磚不同層進行分析研究,如圖2、圖3、圖4所示。
圖片
從殘磚顯微結構和能譜分析結果來看,從原質層、變質層到反應層,爐襯材料中(主要為莫來石相和石英相)的Al2O3/SiO2比值是不斷升高的,說明爐襯材料中的SiO2是向外不斷“流失”的。從動力學上來,耐火材料中的SiO2以固相形式向外遷移是十分困難的。從熱力學上看,在磚內部(變質層)沒有C參與反應的情況下,Cl2與SiO2反應形成SiCl4,以SiCl4氣體形式向外遷移是不可能的。因此,在氯化爐工況條件下,爐襯材料中內部SiO2的“流失”現(xiàn)象只能以SiO氣體形式向外遷移,這可能是SiO2碳熱還原反應所引起。SiO2碳熱還原反應過程如下:
(1) SiO?+2C=Si+2CO(g)
(2) Si+C=SiC
(3) SiO?+3C=SiC+2CO(g)
(4) SiO?+C=SiO(g)+CO(g)
(5) SiO(g)+2C=SiC+CO(g)
(6) SiO(g)+C+2Cl?(g)=SiCl4(g)+CO(g)
(7) SiO?+CO(g)=SiO(g)+CO?(g)△G=△G0+RTln(PSiOPCO?/PCO)
根據(jù)相律,在Si-C-O系統(tǒng)在不變點同時可有5個以上的相:P=3+2=5。即在形成SiC的溫度條件下,此反應開始發(fā)生溫度為1350℃左右,該Si-C-O系統(tǒng)可含有下列單獨物質:C,Si,SiO,SiO?,SiC、CO和CO?。
在C過量并直接參與反應的情況下,反應中不存在CO?。從動力學角度看,基元反應多數(shù)是單分子反應和雙分子反應,三分子反應不多,四分子反應更少,所以除少部分緊密結合、相互包圍的SiO?與C直接通過式(3)所示固相反應生成SiC晶核之外,SiO?與3個C分子同時相遇發(fā)生反應的幾率較小,即式(3)所示反應發(fā)生的程度非常有限,更應被視為幾個加合反應的總反應式。
在Si-C-O系統(tǒng)反應中,C和SiO?為反應原料,Si和SiO是反應的中間產物,SiC和CO為末尾產物。Si的熔點為1410℃,沸點為2355℃,而SiO在1180℃以下任何溫度都不穩(wěn)定,在高溫下以氣態(tài)存在,所以中只存在SiO?、C、CO、SiO、SiC等幾種可能的物相。
可以確定,碳熱還原SiO?的基元反應步驟為:
SiO?+C=SiO(g)+CO(g);SiO(g)+2C=SiC+CO(g)
但事實上有Cl?存在,SiO?碳熱還原的基元反應中,第2步可能沒有按式(6)進行,而是按式(7)進行,從而導致爐襯材料中SiO?的不斷“流失”。在殘磚的表面反應層,SiO?的“流失”可能是按此過程損毀的,這與殘磚反應層顯微結構中看不到SiC是相吻合的。
在C過量但并不直接參與反應的情況下(即PCO/PCO?比值較大),反應中不存在C,那么SiO?碳熱還原的反應將按照式(7)進行。經過熱力學計算,式(7)反應開始溫度為1400℃左右。爐襯殘磚在爐況不正常超溫情況下形成變質層,其中的SiO?的“流失”可能是按此過程損毀的。
三、結論
從前面的分析可知,氯化爐爐襯材料的損毀速度主要受Al?O?-SiO?材料中碳熱還原速度的控制。其損毀過程為:
在磚內部,外部的CO氣體通過材料的孔隙向材料內部擴散,與SiO?發(fā)生碳熱還原反應生成SiO和CO?氣體向外部擴散,到達磚表面時,SiO氣體與表面的C和Cl?反應生成SiCl4氣體,SiCl4氣體向爐內擴散。而CO氣體與SiO?的碳熱還原反應導致材料結構松散,進一步形成外部CO向磚內部滲透的通道,如此反復,直到磚內部CO壓力小到無法與SiO?發(fā)生碳熱還原反應或達不到反應溫度為止。
在磚的表面,SiO?直接與C發(fā)生碳熱還原反應生成SiO和CO,生成的SiO又與C和Cl?反應生成SiCl4,直接向爐內擴散。
外部夾雜著TiO?微細顆粒的TiCl4氣體通過SiO?碳熱還原反應形成的通道,則不斷向磚內部滲透,形成Al?O?-SiO?-TiO?液相(TiCl4對此相圖的影響無資料報道),從而加速材料的結構解體,導致耐磨性能急劇下降。
無論在磚內部或表面,莫來石顆?;揪3至似湓w粒形貌,再次證明了其損毀速度是由碳熱還原速度控制的,與氯化反應速度無關(雖然從熱力學上莫來石容易發(fā)生氯化反應)。
四、氯化爐爐襯的優(yōu)化建議
(一)材料的選用
1、爐襯材料選用氧化鋁含量較高的Al?O?-SiO?系磚是十分必要的。
2、爐襯材料選用高純的電熔莫來石和電熔剛玉為主要原料將可以有效提高其壽命,并可以在更大范圍內容忍操作工藝上的波動。
3、在保證磚熱震性能的基礎上,降低磚的氣孔率和提高熱態(tài)強度(耐磨性能)十分關鍵。
4、選擇合理的制磚級配和結合劑是保證剛玉-莫來石磚在氯化爐上長時間使用的技術核心。
(二)結構優(yōu)化設計
依據(jù)不同部位的損情況進行改造。改造后的爐體結構為:用耐磨性更強的電熔莫來石、電熔剛玉砌筑于進料口位置。而在其他的部位一層采用氧化鋁含量稍低的高鋁磚,二層則和第三層采用氧化鋁含量更低的高鋁磚或粘土磚。
這樣的結構即可以增強爐體的強度,又提高了爐體的氣密性,防止氯氣從砌縫中泄漏,同時也降低使用成本。其維護保養(yǎng)也簡單,每次維護只需要對損壞部分進行替換即可,每次維護后大約可連續(xù)使用一年左右,并且每次的維護時間大約一周,有效的提高的生產效率。
上述結構的改造,是結合爐襯損壞機理及氯化冶金工況進行理論上的優(yōu)化設計,還需要在實踐過程中不斷地改進,在使用壽命和成本上綜合考慮。